
Ancient Beginnings and Early Uses
The history of rubber cutters traces back to ancient civilizations when natural rubber was first discovered. Natural rubber, derived from the latex of certain tropical plants, primarily the Hevea brasiliensis tree, became essential for various utilitarian purposes. Indigenous cultures in Central and South America initially used this elastic material to create waterproof items and rudimentary balls for games.
Early methods of processing rubber were crudely simplistic yet effective. These involved hand tools like sharp stones or bones to cut and shape the sticky substance. Ancient societies recognized the significance of rubber in their daily lives, using it for adhesive, medicinal purposes, and footwear protection, demonstrating an early appreciation for its versatile applications.
The Industrial Revolution and Its Impact
The dawn of the Industrial Revolution marked a significant turning point for rubber use and processing. With industries expanding rapidly, the demand for stronger, more durable materials skyrocketed. As such, rubber's elasticity and resilience came to the forefront, inspiring innovations in rubber cutting and molding techniques.
The emergence of mechanical rubber cutting tools revolutionized this sector. Factories implemented steel knives and saws capable of slicing through larger volumes of raw rubber with enhanced precision. Pioneering industrial machinery facilitated mass production and standardized quality, laying the groundwork for further advancements.
Technological Innovations in the 19th Century
The 19th century introduced transformative technological innovation in rubber cutting tools. As industries diversified, so did the need for more specialized and precise cutting instruments. It was during this era that vulcanization, a process discovered by Charles Goodyear, significantly improved rubber's durability and malleability, making it easier to cut and mold into desired shapes.
Engineers began to design machines specifically for accurate rubber cutting—a leap substantiated by numerous patents granted throughout the period. Precision-driven inventions, including rotary cutters and stamping tools, enabled faster and cleaner cuts, enhancing productivity and resource efficiency within factories.
20th Century Advances and Mechanization
The 20th century witnessed unprecedented advances in rubber cutting technology, paralleling global events. A seminal innovation was the development of automated cutting machines capable of producing consistent, accurate results at higher speeds. Robotics and mechanization transformed operations, reducing human error and improving safety standards.
Material science also played a critical role—new blade materials like tungsten carbide extended tool life and maintained razor-sharp edges longer than traditional steel. The exigencies of World War II drove further acceleration in rubber technologies, with defense applications necessitating robust, reliable components and cutting-edge manufacturing processes.
Computerization and Modern Techniques
With the advent of computer-controlled systems in the late 20th and early 21st centuries, rubber cutting entered an era defined by remarkable precision and efficiency. CNC (Computer Numerical Control) machines enabled intricate designs and rapid prototyping previously unattainable manually. The integration of advanced technologies like laser and water jet cutting offered fast, clean cuts requiring minimal post-processing.
This level of sophistication drastically reduced waste and operational costs while boosting output accuracy. Industry players now leverage CAD (Computer-Aided Design) software to customize products precisely to specifications, ensuring final goods meet stringent quality standards consistently.
Industry-Specific Rubber Cutting Innovations
Modern developments have led to highly specialized rubber cutters tailored for distinct industry requirements. In automotive manufacturing, these ensure perfect sealing components and sound insulation. Aerospace industries utilize them for lightweight, high-performance parts critical to aviation safety and efficiency.
In medical fields, precision is paramount, and custom-designed cutters produce finely detailed, sterilizable elastomers for implants and devices. Diverse needs across sectors drive ongoing refinement and creativity in rubber cutting solutions—a testament to the adaptability of cutting technology to meet dynamic market demands.
Sustainability and Future Prospects
As environmental considerations spotlight sustainability, eco-friendly rubber cutting technologies are gaining traction. Equipment designed to minimize energy consumption, coupled with efficient recycling processes, underscores the industry's commitment to reducing its ecological footprint.
Forward-looking projections anticipate developments in AI-powered machinery and enhanced automation, promising even greater efficiency and fewer resources squandered. This sustainable trajectory aligns closely with global priorities on conservation and waste reduction.
Further Exploration and Reader Engagement
If you're intrigued by the journey of rubber cutters through time, explore interactive timelines and visual aids detailing pivotal milestones. For a deeper dive, consider reading comprehensive studies and historical accounts available online. We'd love to hear your thoughts and experiences with rubber cutting tools—feel free to share anecdotes or ask questions!
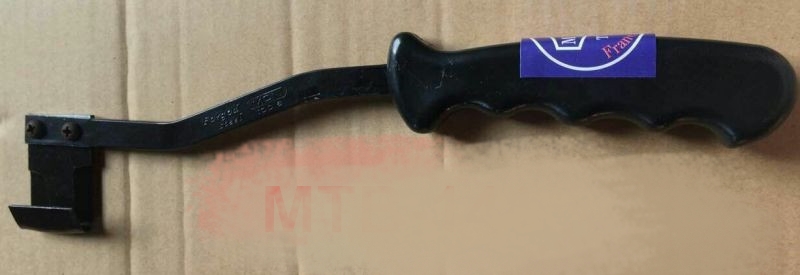