
In the evolving domain of modern manufacturing, the role of precision tools such as rubber cutters has become increasingly pivotal. The dynamic nature of manufacturing means that adaptability and accuracy are paramount, and rubber cutters offer just that—transforming raw materials into finely crafted components critical across various industries.
The Role of Rubber Cutters in Modern Manufacturing
Looking back, the process of rubber cutting has undergone significant evolution over the years. Initially relying heavily on manual techniques, this method was both labor-intensive and prone to human error. This all changed with the advent of automated rubber cutting methods, revolutionizing efficiency and precision in manufacturing. Today’s technology offers an array of advanced rubber cutting machinery that cater to diverse industrial needs.
Understanding Rubber Cutters
There are different types of rubber cutters designed for specific applications including die cutters, laser cutters, and waterjet cutters. Each type comes with its own set of key components and specialized materials, making them suitable for varying degrees of complexity and intricacy.
Technological advancements have played a crucial role in enhancing the capabilities of these machines. Modern rubber cutting tools now boast features like computer numerical control (CNC) systems, which allow for unmatched precision and intricate designs. These innovations make it possible to cut rubber materials efficiently, reducing waste and improving overall productivity.
Applications Across Industries
Automotive Sector
In the automotive industry, custom gaskets and seals made from rubber are essential for ensuring vehicle safety and durability. Precision-cut interior components, such as floor mats and paddings, highlight the importance of rubber cutters in delivering products that fit perfectly within design specifications.
Medical and Healthcare Industry
The production of rubber parts for medical devices underscores the necessity for hygiene and precision. Rubber cutters ensure that each part meets stringent healthcare regulations, maintaining cleanliness and functionality in vital equipment.
Electronics and Technology
In electronics, customized rubber components enhance the durability and functionality of gadgets. From insulating materials to protective casings, rubber cutters enable manufacturers to produce high-quality electronic devices suited for rigorous use.
Benefits of Custom Rubber Cutting
Precision and Accuracy
One of the standout benefits of using rubber cutters is their ability to achieve intricate designs and tight tolerances. This ensures reduced material waste and improved efficiency, key factors in cost-effective manufacturing.
Flexibility in Design
Custom rubber cutting provides remarkable flexibility in accommodating various shapes and sizes. Additionally, these tools facilitate quick turnaround times, allowing rapid prototyping and production to keep up with market demands.
Cost-Effectiveness
Efficiency in material usage and reduction in production time are primary drivers of cost-effectiveness when employing custom rubber cutters. Economies of scale come into play, especially when producing large quantities of custom parts.
Innovations and Future Trends
Integration of AI and Machine Learning
The integration of Artificial Intelligence (AI) and Machine Learning is paving the way for predictive maintenance in rubber cutting machinery. Furthermore, AI-driven adjustments can significantly enhance precision, driving improvements in overall operational efficiency.
Sustainable Manufacturing Practices
Sustainability is becoming a cornerstone of modern manufacturing practices. Eco-friendly materials and recyclable rubber waste products are being integrated into manufacturing processes, aiming for minimal environmental impact while maximizing resource efficiency.
Selecting the Right Rubber Cutter
Choosing the appropriate rubber cutter involves several considerations such as material compatibility, cutting thickness, speed, and efficiency requirements. Additionally, budget constraints and the long-term value of investment should also be factored into decision-making.
Case Studies
Real-world examples abound of successful custom rubber cutting implementations. Industry leaders often share testimonials highlighting how specifically tailored rubber cutters have enhanced operational efficiency and product quality, ultimately contributing to business growth.
Practical Tips for Manufacturers
Maintenance and Upkeep
Regular maintenance is key to preserving the longevity and performance of rubber cutting equipment. Adhering to best practices helps mitigate common issues and extends machine life, ensuring uninterrupted production cycles.
Training and Safety
Operator training and certification are imperative for the safe handling and efficient operation of rubber cutting machinery. Implementing comprehensive safety protocols safeguards not only the employees but also the integrity of the manufacturing process.
Conclusion: The Future of Custom Rubber Cutting in Manufacturing
The future of custom rubber cutting in manufacturing looks promising, bolstered by continuous innovations and advancing technologies. Predictions indicate increased integration of AI and sustainable practices, heralding a transformative era where precision and efficiency reign supreme. As we look ahead, it's clear that rubber cutters will remain instrumental in shaping the future of modern manufacturing.
Discover top-notch Rubber Cutter solutions at Yiwu Xinwang Hardware Firm. We specialize in providing high-quality rubber cutting tools to meet diverse hardware demands. Explore our offerings today!
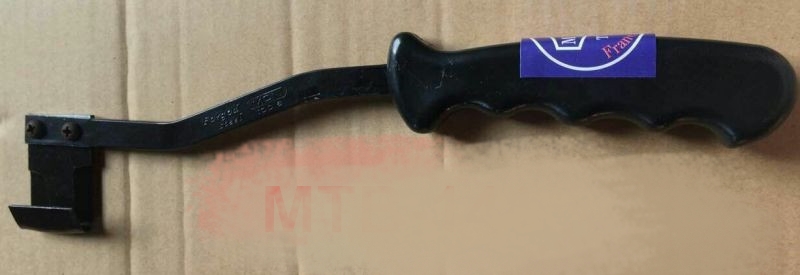